Polymers and why they matter
A polymer is a large molecule made up of repeating subunits derived from molecules of low relative molecular mass, called monomers. Polymers, both natural (e.g. DNA, silk, cellulose) and synthetic (e.g rubber, epoxy resin, polystyrene), play an important role in everyday life due to their range of properties.
What is polymerization and polymer synthesis?
Polymerization chemistry is the process of reacting monomer molecules together in a chemical reaction to form polymer chains or three-dimensional networks.
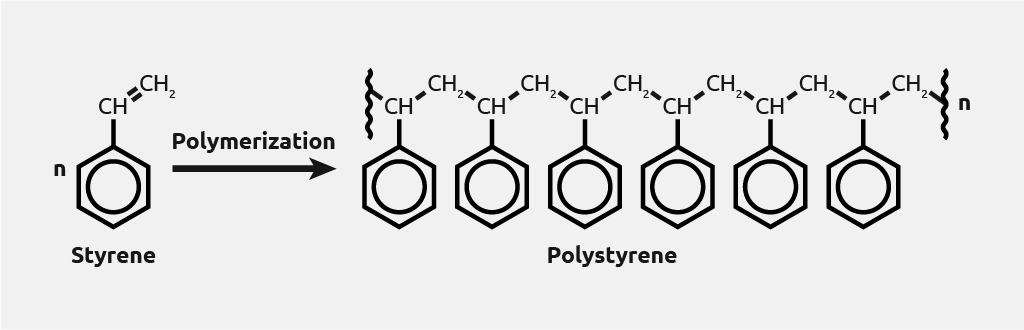
There are many forms of polymerization and different systems exist to categorize them.
There are many ways to classify polymerization reactions as well as the polymers that are formed:
Polymerization classification
- Addition (chain reaction) polymerisation (examples: Teflon, PVC)
- Condensation (step growth) polymerization (examples: Polyester, proteins)
Monomer Classification
- Homopolymers: A+A+A+A… -> AAAA… (Polystyrene, Kevlar)
- Copolymers: A+B+A+B… -> ABAB… (Nylon, nitrile rubber)
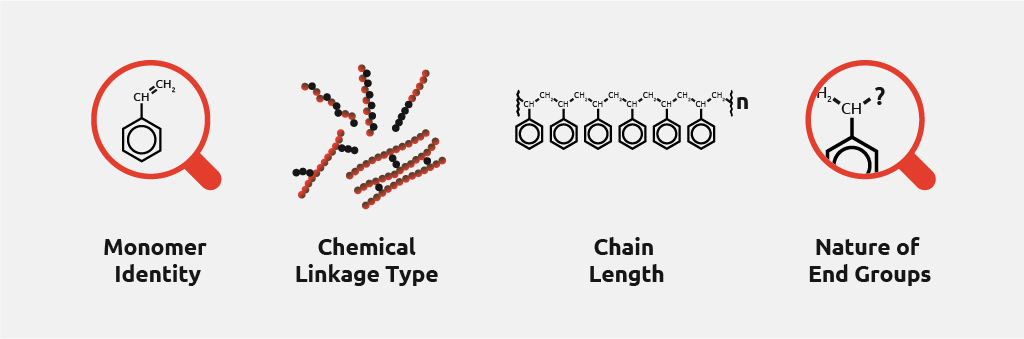
Challenges faced by polymerization chemists
Polymer synthesis is a complex procedure that can take place in a variety of ways. The main challenge faced by polymerization chemists is to achieve the desired polymer size and polydispersity (as monomer identity, and thus nature of end groups, are typically pre-defined).
Polymer size – The average number of monomer units in each polymer chain. Different average chain lengths may have different properties.
Polydisperisty Index (PI) – Quantifies the “breadth” of the molecular weight distribution of the polymer sample. Can affect the suitability of a polymer for a desired application if specific properties (associated with a given chain length) are required.
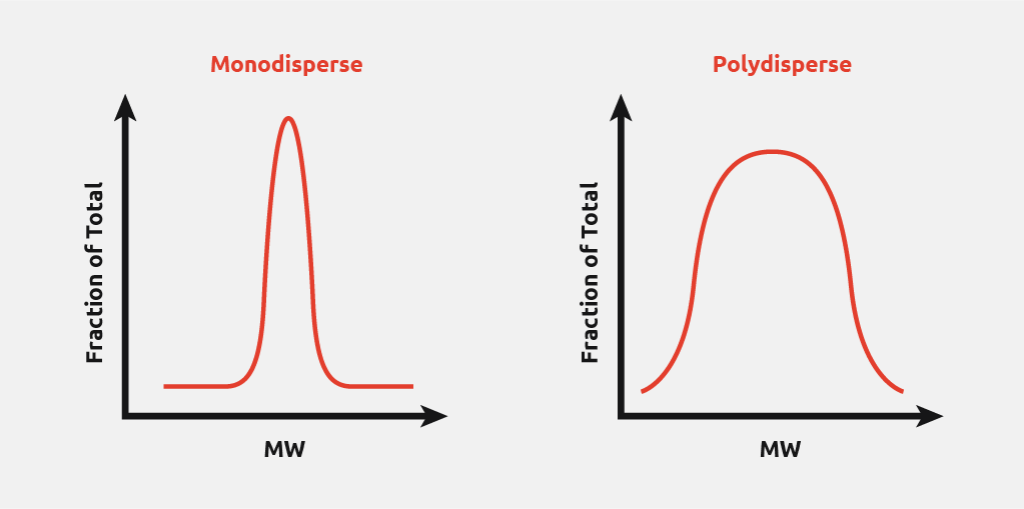
In order to achieve the desired polymer properties, it is important to understand the polymerization reaction, study practical ways of controlling the reaction, and to select the right chemical reactor for the chemistry.
Click here to discover Syrris products used in polymerization studies
Conducting polymerization with batch chemistry techniques
Polymerization chemistry has traditionally been performed using batch chemistry methods, carefully controlling reagent concentrations, catalyst loadings, temperature and time to provide polymers with the desired properties.
Automated jacketed lab reactors such as Atlas HD automated jacketed reactor offer excellent control over polymerization reaction parameters, such as temperature, pressure, mixing, concentrations, and reaction times. This advanced control enables chemists to reduce the polydispersity of their reactions and achieve batch-to-batch reproducibility. The geometry of jacketed reactor vessels often mimics those at pilot plant scale, providing chemists with greater confidence in the feasibility of scaling up their chemistry.
Further reproducibility can be achieved through automation of the experimental protocol.
Reaction calorimetry for polymerization scale-up safety studies
Reaction calorimetry allows polymerization scientists to see the polymerization rate and the overall polymerization reaction profile of their chemistry, helping them to determine the enthalpy of reaction and ultimately helping to determine the safety of scaling up their reactions.
Polymerization customer story
Medtronic controls polymer synthesis with Syrris Atlas jacketed reactor
Medical device manufacturer, Medtronic, Ireland, has invested in two Atlas HD Potassium jacketed reactor systems from Syrris for the synthesis of polymers under strictly controlled conditions.
We need to keep tight control over our polymer synthesis processes and this, together with the simplicity of the system, was the main reason for selecting the Atlas HD Potassium.”
Syrris in polymerization publications
Syrris products have been used in many polymerization studies, including:
Polymerization in Batch chemistry:
-
Factorial design to obtain magnetized poly(ethyl acrylate co-divinylbenzene)
First published: 04 July 2019 | https://doi.org/10.1590/0104-1428.04118
This publication used an Atlas HD jacketed reactor to create magnetized polymers by capturing magnetic particles within a polymer matrix.
-
Cationic versus anionic core-shell nanogels for transport of cisplatin to lung cancer cells
First published: 15 July 2019 | https://doi.org/10.1016/j.colsurfb.2019.110365
This publication used an Atlas HD jacketed reactor to synthesise polymeric nanogels for use in the drug delivery of cisplatin.
Polymerization in Flow chemistry:
-
Continuous Flow Polymer Synthesis toward Reproducible Large‐Scale Production for Efficient Bulk Heterojunction Organic Solar Cells
First published: 21 August 2015 | https://doi.org/10.1002/cssc.201500850
This publication used an Asia flow chemistry system.
-
Continuous-Flow Synthesis of Regioregular Poly(3-Hexylthiophene): Ultrafast Polymerization with High Throughput and Low Polydispersity Index
First published online: 15th July 2014 | https://doi.org/10.1556/JFC-D-14-00009
This publication used an Asia flow chemistry system.