Syrris Asia system for efficient styrene polymerization
Professor Ardson dos Santos Vianna, Department of Chemical Engineering, São Paulo State University, is using a Syrris Asia Flow Chemistry System to enhance the efficiency of styrene polymerization in an effort to improve the production of polystyrene.
When I saw the Syrris Asia Flow Chemistry platform, it was clear that the equipment was well constructed and a better fit for my research than other alternatives on the market.”
Continuous flow styrene polymerization
Polystyrene is a widely used plastic for a range of applications, particularly as packaging materials due to its inertness and resilience. However, the introduction of other lower cost materials has driven new efforts to improve the efficiency of the production process of polystyrene.
The polymerization of styrene is typically performed by mixing the styrene monomer with an inhibitor such as benzoyl or peroxide; the inhibitor decomposes to form radicals that attack the double carbon bond of styrene and cause polymerization, and it is this conversion that Professor Ardson dos Santos Vianna improved using flow chemistry methods.
Professor Ardson’s continuous flow polymerization process employs millireactor and microreactors and enables good conversion of the styrene monomer into a high molecular weight polymer with a narrow, reproducible molecular weight distribution and improved productivity compared to batch or tubular flow reactors.
Styrene polymerization is a process optimization compromise as not all parameters complement each other; improving the molecular weight distribution may result in a reduction in the conversion of styrene monomer to polymer, for example. Working with the Asia Flow Chemistry System enabled Professor Ardson to perform fast screening of reaction parameters, greatly speeding up the optimization process. Additionally, the minute changes in temperature, concentration, residence time, and inhibitor mass that continuous flow provides enabled Professor Ardson to narrow down the optimum reaction settings.
- Aggressive reaction parameters, such as high temperatures (115 °C), high monomer concentration, and reduced solvent use led to increased conversion rates (up to 66.8%)
- Increasing incidence time of reaction and initial mass of initiator led to increased conversion
- However, the greatest molecular weight was achieved with a conversion rate of just 27.9%, while the largest conversion rate of 66.8% yielded significantly lower molecular weights
Professor Ardson said: “I have been working in flow chemistry for the past five years, studying solution and emulsion polymerization and enzymatic degradation. My goal is to study fluid dynamics and develop 3D computational models to predict the molecular weight distribution and improve polymerization efficiency.”
“Previously, I worked with a homemade continuous flow set-up. I already had a long-standing relationship with Syrris, and it made sense to turn to the company for assistance. When I saw the Syrris Asia Flow Chemistry platform, it was clear that the equipment was well constructed and a better fit for my research than other alternatives on the market, which led me to purchase a system with both a 250 mL microfluidics chip and a 4 mL tubular reactor. This has been critical to my current research, which explores the complexity involved in optimizing various parameters, such as temperature, concentration, residence time and initiator mass. The system is easy to use, and I appreciate its modular design, which will allow me to easily upgrade in the future.”
Speciality Chemicals Magazine Editorial
Professor Ardson’s pioneering work has been featured as an editorial in the May edition of Speciality Chemicals Magazine, and forms the base of our blog post “Improving polystyrene production with continuous flow chemistry“
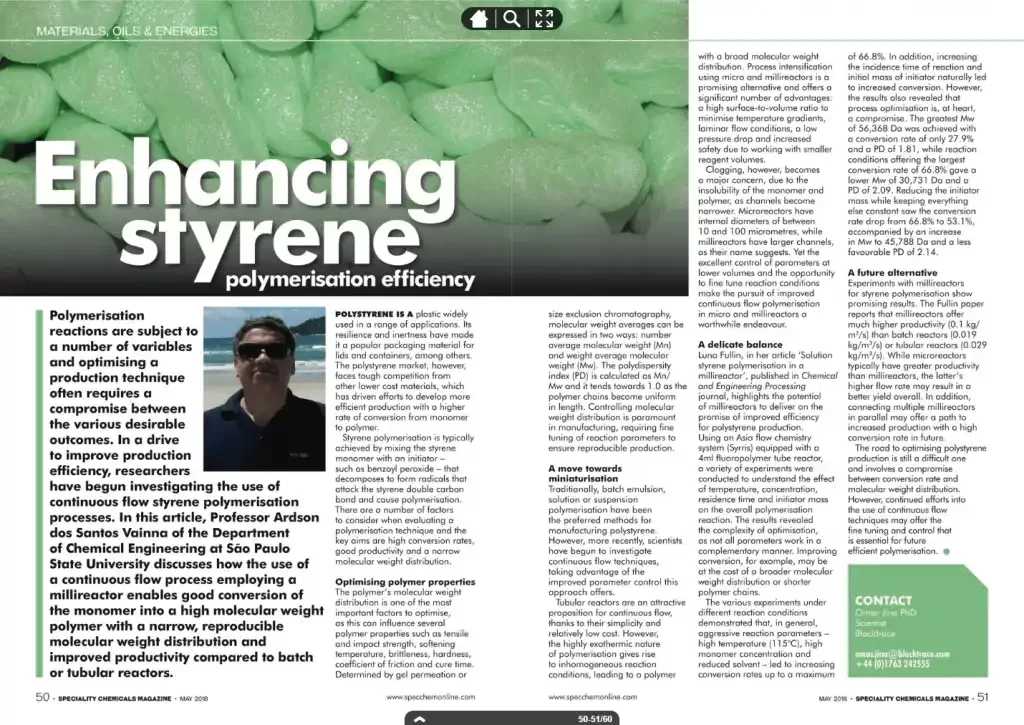
Interested in learning more about polymerization, its uses in industry, and methods of performing polymerization chemistry? Discover our Polymerization Applications page here.