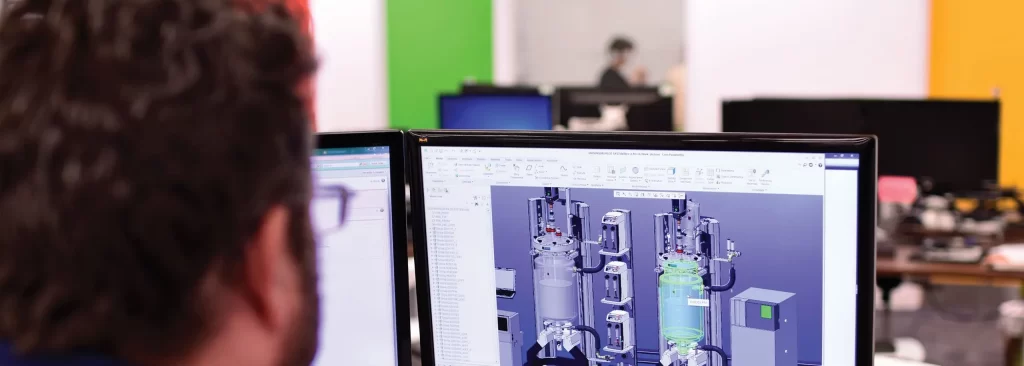
Custom Reactor Systems and Pressure Reactor Systems
We understand that all labs are different, so while we’ve designed our products are designed to be as flexible as possible, sometimes you’ll need something unique to your laboratory or application.
Custom reactor system overview
Discover our custom solutions.
The Syrris R&D Team collaborates with chemists and chemical engineers across various industries to design, prototype, test, and build custom solutions for batch, flow, and scale-up chemical reactor systems.
Our Custom Team, along with Regional Sales Executives, guide clients through the custom product process, ensuring all equipment meets specifications, quality standards, and relevant compliance.
We cater to customers from lab-scale facilities to pilot plants, offering a range of materials, sizes, including stainless steel options. Contact us today to learn how we can tailor a custom reactor system for your lab or industrial needs.
Available custom parts: reactor vessels, pressure vessels, and more
Over the years the Syrris R&D Team has developed a range of custom parts – from stirrers, pressure vessels, condensers, and other glassware – through to entire custom systems. We manufacture our own glassware so have complete flexibility.
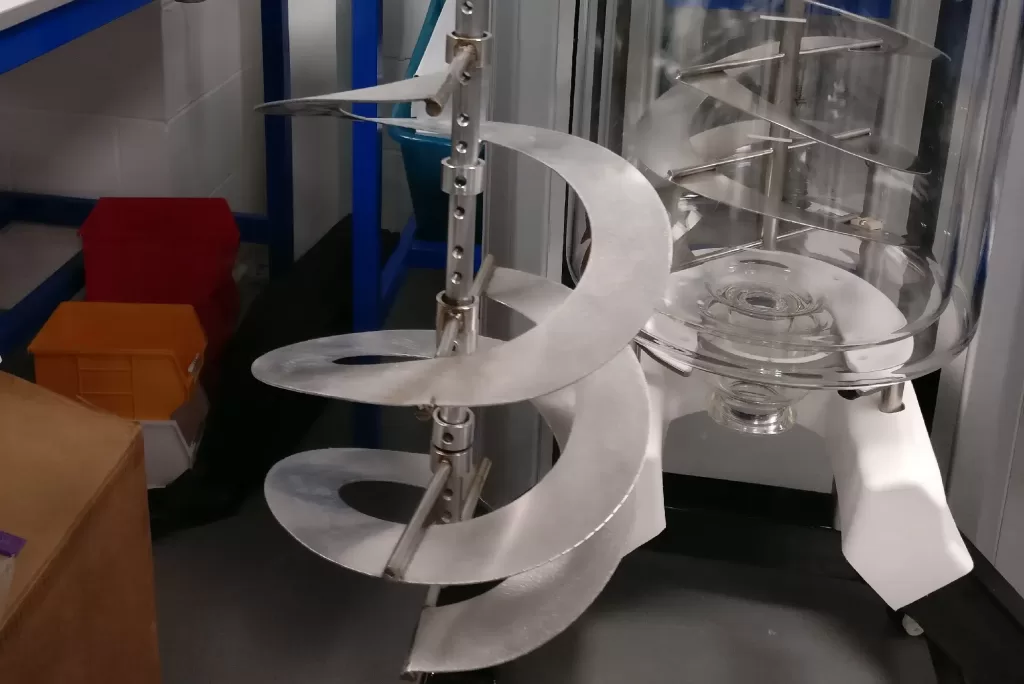
How we engineer custom parts: From concept to fabrication
Many custom parts are simple variations on our existing parts – a shorter stirrer shaft or extra ports on a lid, for example. Some customers, however, require far more complex custom parts for their jacketed reactors or flow chemistry systems, such as automated bottom outlet valves (BOVs) or completely customized stirrers.
For these more complex custom parts requirements, the Custom Parts Team at Syrris uses a 4-step process when working with customers to produce custom parts for our batch and flow chemistry systems.
-
Step 1: Feasibility study and initial specifications
After initial discussions with the customer about what they’re trying to achieve, the Custom Parts Team perform a feasibility study to determine if it’s possible, how the part would need to function to perform its role and generate CAD drawings of the part.
-
Step 2: Prototyping and quality testing
Following approval from the customer on the feasibility study, the Custom Parts Team manufacture a prototype part to test it. During this part of the process, the customer may visit the Syrris office to see the part in action, or we’ll send a video recording to the customer. Several prototypes may be created to determine the best design for the custom part.
-
Step 3: Final design and code compliance
Feedback generated from the prototyping stage is used to determine the final CAD design of the custom part, which is then sent to the customer for approval. This stage ensures that all design elements adhere to code requirements, guaranteeing safety and compliance. Our engineering team meticulously reviews the specifications to certify that the equipment or part meets all industry standards.
-
Step 4: Production and certification of custom reactor projects
Following the customer's final design approval, manufacturing drawings are completed, and then the custom parts are manufactured. The full system, including the custom part, is built, and it is fully tested before being shipped to the customer. If required, instructions for use/assembly are generated and added as an addendum to the system's operating manual.
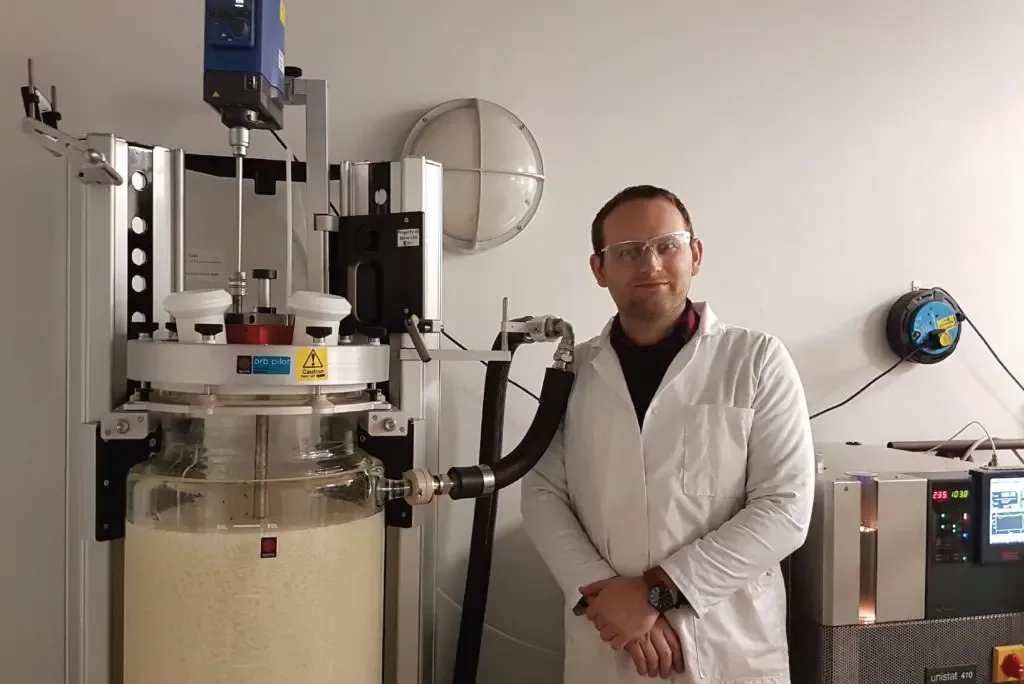
Customer story
Improving sustainability in commercial laundry with a custom Orb Pilot system: Syrris’ Custom Parts Team worked with Robert Bird, R&D Project Manager at Xeros, to develop a custom double-helix stirrer and gearbox, specifically designed to fit a 50 L Orb Pilot scale-up jacketed reactor vessel.
Dr. Omar Jina, Chief Commercial Officer
Contact us for more information on custom products for your research needs
Interested in how Syrris could provide you with the custom parts your lab needs? Then use the contact form to speak to us about your specific applications and requirements.
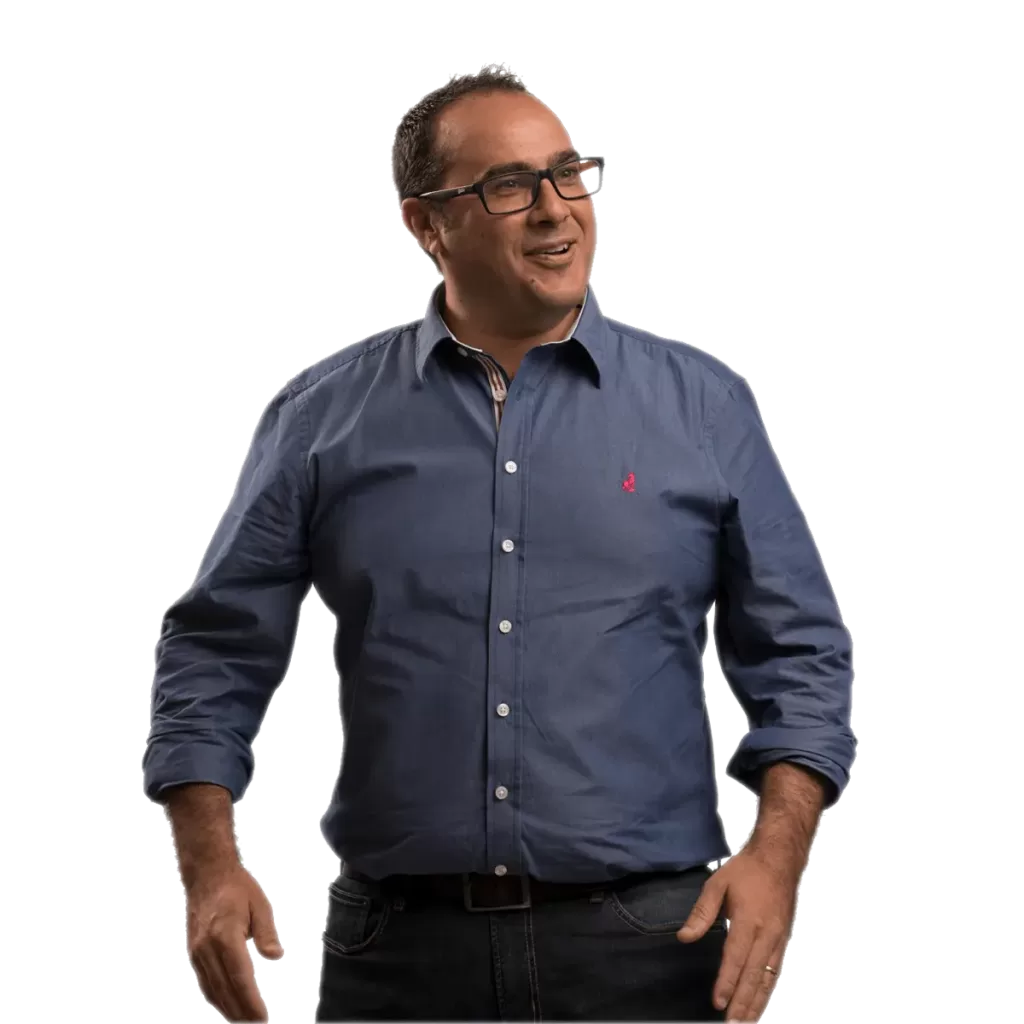