Plug Flow Reactors: An Overview
What is a Plug Flow Reactor?
The question often asked of us is how does a plug flow reactor differ from a tubular reactor? The truth is that they are both the same and different. The plug flow model describes an ideal, and the terms are commonly interchangeable.
Continuous flow regimes or the plug flow model if you’re a chemical engineer is a model used to describe chemical reactions in continuous, flowing systems of cylindrical geometry (a flow reactor in our case).
The Plug Flow model considers our fluid flowing through our reactor as a series of plugs (or slugs), each extremely small, with its own composition and perfectly mixed in the radial but not axial direction (forward or backward). In this sense, we have a series of infinitesimally small reactions flowing through our system.
We can show this “plug flow” behaviour, where each coherent ‘‘plug’’ has a given length (dx) and volume (dV) (Figure 1), traveling in the longitudinal direction of the reactor where mixing and diffusion does not occur in the direction of the flow path.1,2
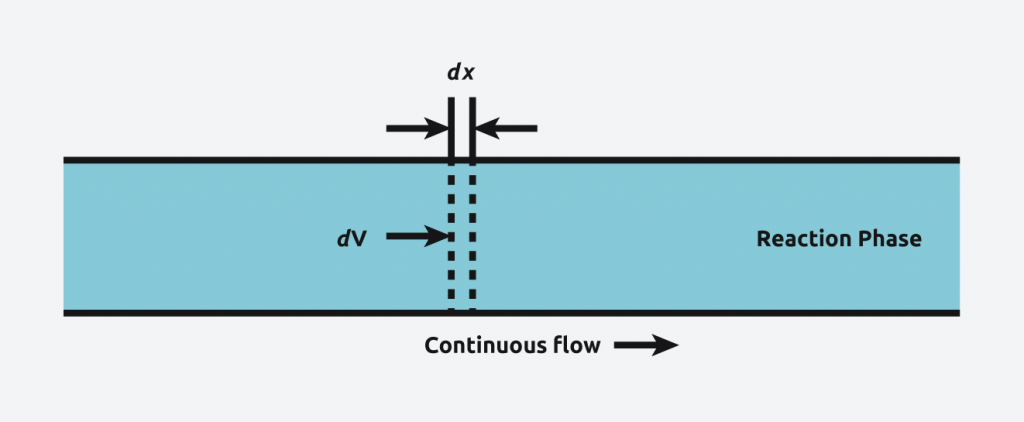
This is not the only consideration when we think about running continuous flow experiments as this ideal plug flow reactor model assumes that we have a steady state, that no mixing occurs between plugs, we have a constant density and that only one reaction occurs. Some of these assumptions are considered later.
Residence Time Distribution
While the Plug Flow model is a useful tool to estimate the behavior in a flow reactor, a typical flow reaction does not follow the “ideal”. A “non-ideal” plug flow reactor has a residence time distribution that is a narrow pulse around the mean residence time distribution. The Residence Time Distribution (RTD) of a reactor considers the mixing that occurs. In a plug-flow reactor there is no axial mixing, in a continuous flow reactor this is not the case. Mixing in a plug flow reactor can be illustrated when we consider segmented flow.
Segmented Flow
Segmented flow is defined by alternated segments of liquids or gases, for most chemistry applications this is the reaction phase and a carrier fluid phase (Figure 2). While a plug flow reactor presents infinite number of plugs with infinitesimal volume, segmented flow presents discrete slugs (DX) with defined volume (DV).1 Carrier fluids can be both liquid or gas but are generally the same solvent that the reaction is performed in to minimise solubility issues.
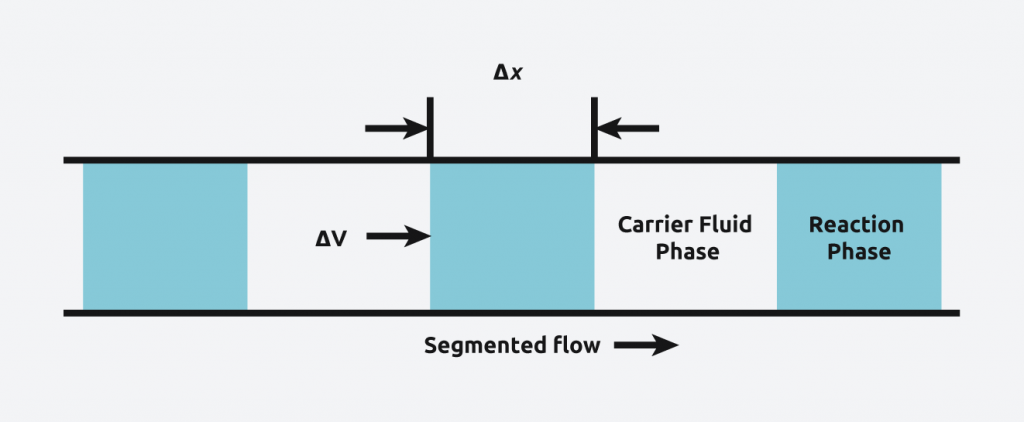
We can use this principle to allow us to introduce small aliquots of our reactants to create “segments” to screen both reaction conditions and to generate arrays or libraries of compounds.
For ideal cases, no diffusion is expected, and the concentration of solute doesn’t change (3 – a). In non-ideal cases (i.e. real cases), dispersion and diffusion phenomena can take place (mainly in the longitudinal direction) and the outcome is often a mixing between the reaction and carrier slugs, forming a blurred region in the front and in the back of slug reactions (3 – b).1,2 This effect causes a solute concentration gradient and can affect the reaction rate (for concentration reactions dependent) and the residence time of slug.
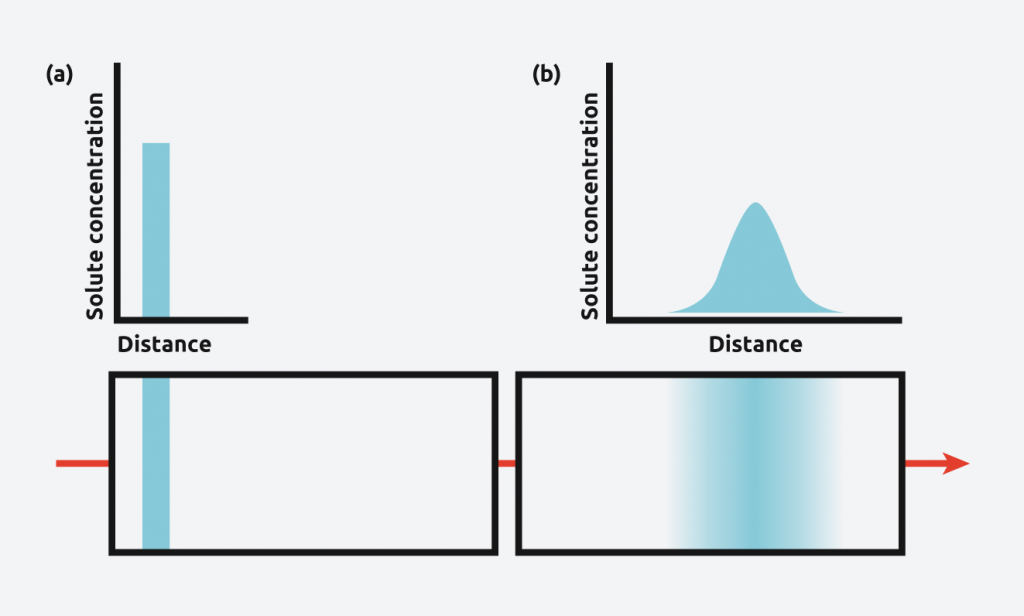
Plug Flow Reactor Design
In the simplest terms, a plug flow reactor is a reactor constructed of a capillary of some type. This can be a simple tube or a channel etched into a plate. Continuously stirred tank reactors (CSTR) can also be described as plug flow reactors.
Continuously Stirred Tank Reactor
CSTR’s are chemical reactors considered as a hybrid of a traditional batch and a continuous flow reactor. The continuous stirred tank reactor (CSTR), used to combine chemicals in a batch-type vessel, this device gradually meters reactants in the right ratio, contains the reaction and permits removal of the new product, often without disrupting the reaction.
There are few controls on a CSTR that can be used to control throughput and the purity of the product. The feed rates of the pumps used to inject reactants into the CSTR, temperature control and stirring.
Chip-based Reactors
These type of reactor ranges from small glass teched microreactors to larger “plate” based reactors of silicon carbide for manufacturing. They offer the best heat transfer characteristics from their extremely high surface area to volume ratios. Their manufacture offers advantages in the wide range of geometries that can be etched including complex mixing sections.
Coil-based Reactors
These reactors are typically made from a length of tubing that can be heated or cooled via a dedicated thermostat unit. Their construction is generally PTFE, PFA or Stainless Steel depending on the temperatures and pressure required and the associated chemical compatibility of the reaction. These are the most used continuous flow reactors due to their lower cost compared to chip-based reactors.
Packed Bed Reactors
If heterogeneous catalysts or reagents are required then packed bed reactors, or solid-phase reactors, are generally used. These are commonly made up of a column or cartridge constructed of glass or stainless steel. The solid reagent is packed into these, and the reaction solution is passed through the column. There are several advantages of these reactors, the molarity of the reagent is much higher, and it removes the need for separation on completion of the reaction.
Uses of Plug Flow Reactors in flow chemistry
Plug flow, or continuous flow reactors have a wide range of uses and applications depending on the type selected.
Lower-volume chip-based reactors with volumes <1000 ml are used when the chemistry has a short residence time or when producing material on a small scale. Highly exothermic reactions for example are often extremely fast and small-volume reactors are ideal for fast residence times. Inversely when low quantities of material are required a small reactor volume and low flow rate is ideal to minimise dispersion.
Larger volume chip (or plate) based reactors find the most use in the manufacture of multiple kilograms of material. Their excellent heat transfer properties mean they are well suited to handling the high mass transfers required to produce large quantities of material. Another advantage of plate-based flow reactors is that they can be stacked together. This approach to scaling out rather than scaling up where the reactor volume is increased means that the reactor characteristics can be maintained.
Coil (or tube) based reactors are most commonly used for their lower cost. Their construction allows for a range of reactor volumes making them extremely versatile. Perfluoropolymer tubing is used for lower-temperature reactions where cryogenic temperatures are required for highly exothermic reactions. When higher temperatures and pressures are required stainless steel or Hastelloy is often used. Reactors of this construction can access temperatures <300oC and 300 bar pressures easily lending themselves to applications in the gaseous phase and for reactive gas chemistry.
Packed-bed (or solid phase) reactors are used where reactions containing solids are necessary. Pumping solids is not ideal in a flow reaction so when heterogeneous catalysts or reagents are required these reactors are used. These reactors contain the solid material effectively allowing for a wide range of reactions. Historically solid-supported reagents were most commonly used but recent advances have seen safe, robust uses of reactive metals for Grignard and zincate formations using magnesium and zinc respectively.
Continuously stirred tank reactors come into their own when suspensions of some type are involved. Batch reactors have no limits on the solid composition, and this helps CSTRs. CSTRs are often used for continuous crystallization processes where the particle size can be controlled over a cascade of reactors. Systems connecting several CSTRs are used when the reaction is very slow. Multiple CSTRs can also be used when two immiscible liquids or viscous liquids are present and require a high agitation rate.
Advantages of Plug (Continuous) Flow Reactors
There are many advantages of using a plug flow or continuous flow reactor over a traditional batch reactor. Selecting the correct type of flow reactor for the chemistry and application is key. Whatever the reactor type there are some fundamental advantages of continuous flow reactors.
- Efficient Residence time control – this is a direct function of reactor volume and flow rate.
- Efficient Temperature Control – high surface area to volume ration promotes efficient heat transfer
- Efficient mixing – if under laminar flow conditions mixing is reproducible.
- Limited batch-to-batch variation – the whole reaction sees the same reaction conditions.
- No back mixing
- Direct scalability – the same reactor can be used to produce a range of quantities
- Energy efficiency – the continuous nature avoids stopping and starting as in batch reactions.
Flow Chemistry Equipment by Syrris
The Syrris Asia Flow Chemistry System is a range of award winning flow chemistry modules that enable the widest variety of flow chemistry applications.
Contact our team of specialists to find out how the Syrris Asia Flow Chemistry System could help your chemistry applications.
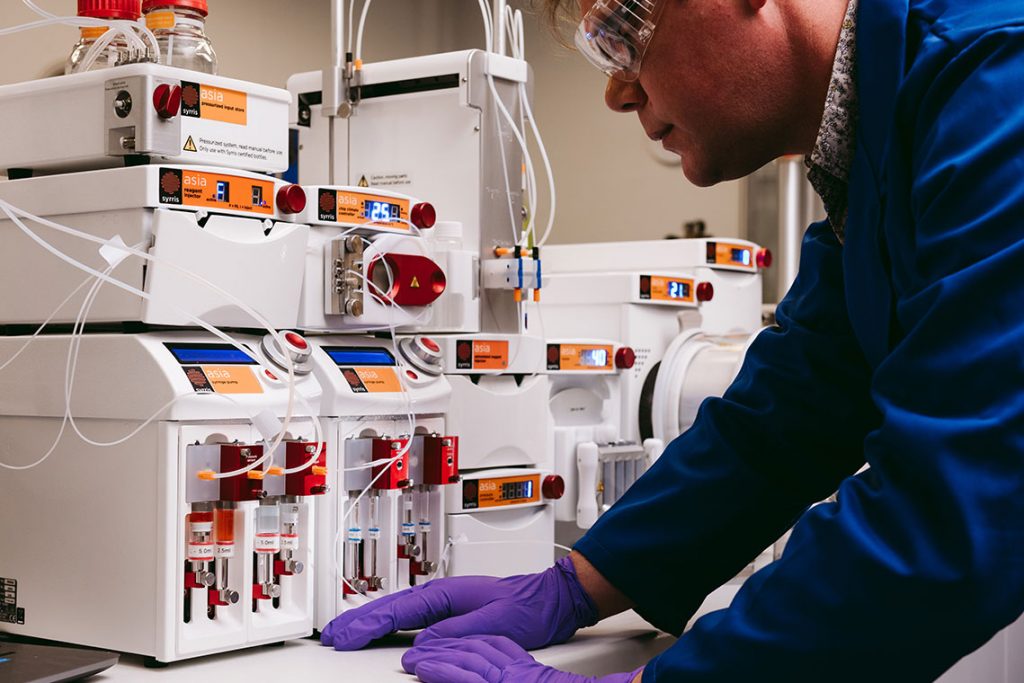