What is flow chemistry?
Flow chemistry, sometimes referred to as “continuous flow chemistry”, “plug flow“, or “microchemistry”, is the process of performing chemical reactions in a tube or pipe. Reactive components are pumped together at a mixing junction and flowed down a temperature controlled pipe or tube.

-
Flow rate, residence time, reactor volume & production rate
In a flow reactor, the residence time (i.e. the amount of time that the reaction is heated or cooled) is calculated from the volume of the reactor and the flow rate through it.
Residence time = reactor volume / flow rate
In this way, Syrris systems (such as Asia) are able to operate with reaction times from a few seconds to a few hours and can be used to synthesize mg to kg quantities in 24 hours.
-
Diffusional mixing in microreactors
In Syrris microreactors, reagents do not mix by turbulence (as in a batch reactor); instead, the reagents mix by diffusion. Because the distance across the chip reactor channel is approximately 200 μm, the time taken for reagents to completely diffuse is from a few milliseconds to a few seconds.
-
Pressurizing & superheating reactions
Syrris flow systems can be easily pressurized up to 20 bar. This allows reactions to be performed at temperatures much higher than atmospheric reflux, enabling faster and often cleaner, higher yielding reactions. Typically, solvents can be heated 60 to 150°C above their boiling point. Therefore reaction rate increases of the order of 1000-fold are possible.
Examples of the superheating effect that can be achieved include:
- DCM @ 158ºC (vs 40ºC at atmos. press.)
- THF @ 193ºC (vs 66ºC at atmos. press.)
- Dioxane @ 240ºC (vs 100ºC at atmos. press.)
-
Pressurizing with gas evolution
Applying pressure to a flow reactor also suppresses the evolution of gas. (This is beneficial because if gas bubbles are formed they can propel the reaction mixture out of the reactor leading to uncertain residence times).
-
Temperature control
The surface area to volume ratio of the reaction mixture in a Syrris reactor is 1000s of times greater than a round bottom flask. Thus heat can be transferred to or from the reaction mixture much more rapidly than in a batch reactor. Greater temperature control can, therefore, be maintained for exo- or endothermic reactions improving consistency and yield.
-
Running sequential reactions
Asia allows a number of reactions to be performed in a serial fashion. One reaction directly follows another and because of the “plug flow” environment the first reaction is simply pushed out and cleaned by the second.
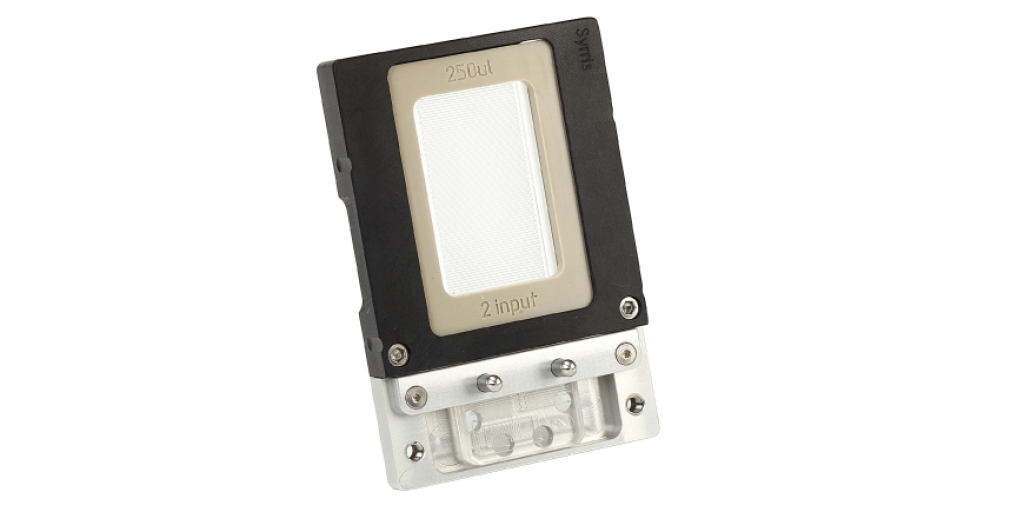